日産伝統の横浜工場でGT-Rの“心臓”を見た 【GT-Rエンジン生産ライン見学取材会】
2008/03/21
■匠のこだわりと技術が生み出すハイパフォーマンスエンジン
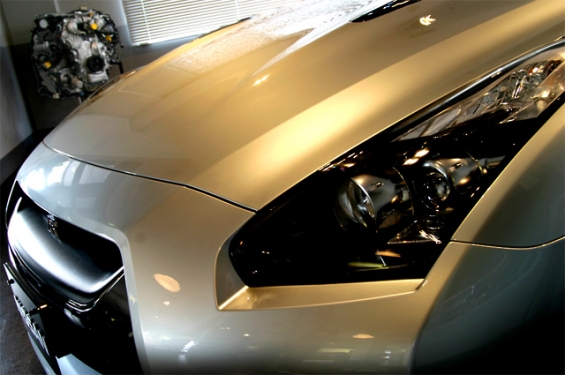
2007年12月にR35型となったGT-Rは「誰でも、どこでも、どんな時でも最高峰のパフォーマンスを」を掲げ、日産が考える新しいジャンルのスーパーカー像を具現化したモデル。そんなGT-Rの心臓部に収められているエンジンがどのように作られているのか。GT-Rファンならずとも気になりますよね?そこで横浜工場で行われたGT-Rエンジン生産ライン見学取材会に参加してきました。
取材会が行われた横浜工場では、GT-Rに搭載されているVRエンジンのほかに、VKエンジン(シーマ、プレジデントなど)、QRエンジン(エクストレイル、プレサージュなど)、MRエンジン(デュアリス、ラフェスタなど)、YDエンジン(エクストレイルの海外仕様)の計5エンジンが生産されています。
VRエンジン以外の4エンジンは、基本的にオートメーション(無人機械)による流れ作業で組み上げられて行きます。一部工程や最終段階では人間の手を介して作業やチェックが行われますが、全工程の約40%ほどを機械作業とすることで作業・生産効率の向上を図っています。また工場内では、組み立てに必要な材料を積んだ無人の運搬車が行き交う光景も見られます。
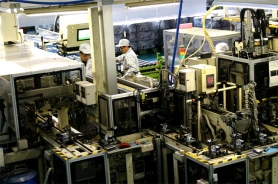
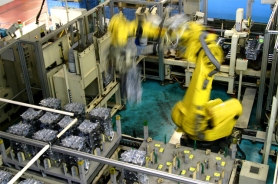
↑VRを除くラインは部品がベルトコンベアで流れて来る(左) 作業・生産効率アップのため、工場内の至るところに無人機が見られる(右)
これは「エンジン生産」という言葉に対して思い浮かべるごく一般的な光景だと思います。ではそんな一般的なエンジン生産ラインと、480ps/60kg-mを発生するハイスペックエンジンの生産ラインとでは何が違うのか。一言で表現するならば“すべて”と言えます。■徹底した環境と高い技術からGT-Rの心臓は生み出される
GT-Rのエンジン生産は、従来のオートメーションによる自動化されたライン生産ではなく、日産最高峰の技術をもった「匠」が手で組み上げていきます。その“匠”に選ばれるのは、エンジン組み立ての分野で長い経験と高い品質意識をもち、さらに担当部署の監督推薦を受けたわずか30名のみ。高水準の品質を保つため、わずか30名という熟練作業集団の形態を取っているのです。さらに生産環境にもこだわりがあります。クリーンルームと呼ばれる組み立て室内は、23℃±2℃、湿度70%以下で気温/室温が徹底的に管理されています。これは冬と夏など季節間での生産誤差をなくすためと、エンジン個体の性能誤差をなくすためだそうです。
作業者は静電気防止の作業服と専用シューズを履き、エア(高圧空気)中に混じるチリやホコリ、水分を付着させないよう電動工具で作業を進めていきます。
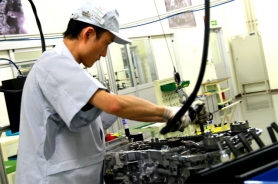
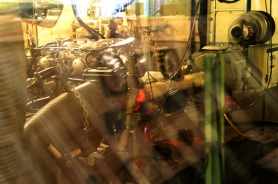
↑豊富な知識・経験をもつ匠により組み上げられていくVRエンジン(左) テストベンチでは高温によりエグゾーストが赤く色づく様子も(右)
この環境下で匠一人一人が370種類にも及ぶ構成部品を1機のエンジンに仕立て上げていきます。VRエンジンの生産ラインは他とは違い、工程によって担当が分かれているのではなく、一人の匠が 1.クランク 2.ピストン 3.ヘッド 4.タイミングチェーン 5.デフの5工程すべてを担当します。エンジン1機を組み上げるのに要する時間は100分。昼夜合わせて1日に生産できる数はわずか50機だけと、スーパーカーにふさわしい珠玉のエンジンと言えるでしょう。エンジンが組み上げられた後には、MTB(モータリングテストベンチ)と呼ばれるエンジンテストに入ります。7.8Lのエンジンオイルが注入された後、専用パレットに載せられテストを行っていきます。このテストでは、レッドゾーン(6400rpm)までの回転域を全13ステップの回転数に分け、1時間にわたり徐々に回転を上げていき、油・水温や振動、水漏れなどのチェックを行います。このテストを通過して、やっと1機のエンジンが完成したことになります。この後エンジンは栃木工場へ運ばれ、サスペンションや内装部品などとともに組み上げられ1台のGT-Rが生まれます。
エンジンの生産が行われている横浜工場は、1933年に日産自動車が産声を上げた記念すべき場所でもあります。その歴史的な場所で、世界に誇る名車の心臓部が生産されているということがまた、日産のGT-Rに対するこだわりや歴史、ロマンを生み出しているとも言えるでしょう。
<カーセンサーnet編集部・フクダ>
日刊カーセンサーの厳選情報をSNSで受け取る
日産伝統の横浜工場でGT-Rの“心臓”を見た 【GT-Rエンジン生産ライン見学取材会】/旬ネタ
あわせて読みたい
先代BMW 3シリーズ(F30型)を買うなら、総額150万円以下が狙い目だ!
9年連続エンジン・オブ・ザ・イヤー2.0~2.5L部門賞を受賞した「2.5L直列5気筒TFSIエンジン」搭載の狙い目モデル3選
閑静な住宅街に潜む、跳ね馬と闘牛がいるガレージ【EDGE HOUSE】
【名車への道】’14 BMW i8
アルピナマジック!~大人の車好きがたどり着く、ひとつの極致~【カーセンサーEDGE7月号】
本場ドイツの名門レース「DTM」が、再び注目を集めるワケ!【EDGE MOTORSPORTS】
残された時間はあとわずか!? 「大排気量エンジン×MT」という歓びを味わえるオススメモデル
手ごろなライトウェイトFRスポーツだったマツダ ロードスター(2代目・NB型)も値上がり傾向。狙うなら今しかない!
【試乗】新型 BMW 2シリーズ グランクーペ│前輪駆動で室内空間向上も、今までとは一味ちがう鋭さの増した駆け抜ける歓びを備えた1台!
アマチュアからの人気が高い量産車ベースのカテゴリー「GT4」、GT3とは違うその魅力とは?【EDGE MOTORSPORTS】